Forklifts for Textile Industry
Forklifts for Textile Industry comprises machines that come with lifting capacity from 1250 kg to 2000 kg and in lifting height of up to 7 meters. The different operating configuration of forklifts makes these perfectly suit the specific needs of the customers. We make these available with power options of LPG, diesel, battery-operated in variations like truck-mounted forklifts, sit-down forklifts, stand-on forklifts, material handling forklifts, walk-behind forklifts and others. Other than these machines we also offer support in form of parts, maintenance as well as the support of forklift attachments like paper roll clamps, double pallet handlers, carton clamps, fork positioners, push-pull attachments, multi-purpose clamps, multiple load handlers and others as demanded by customers.
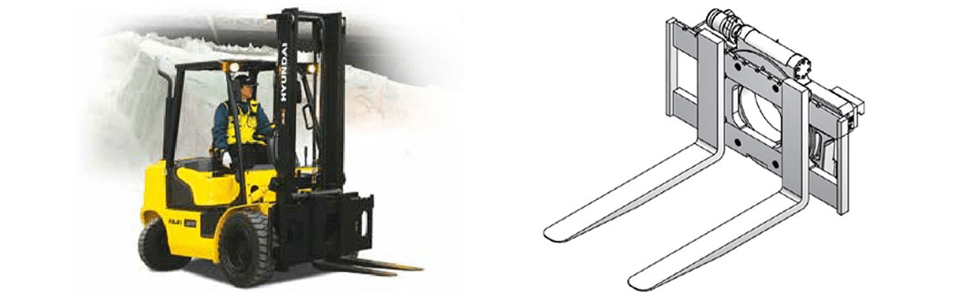
Materials handling in spinning mills
Materials handling covers movement and storage of everything in and around an establishment. The ideal factory would have an absolute minimum of materials handling and hence more use of mechanical appliances. The shortage of labor and increasing wages cost demand the most efficient use of labor. Proper materials handling offers the opportunity for improving productivity, reducing materials wastage, minimizing industrial accidents, reducing man-power, etc.
While determining the choice of equipment, the following factors should be taken into account:
— Mode of arrival and dispatch of materials.
— Type/shape of materials to be transported.
— Amount of materials to be handled in unit time.
— Storage operations and the time materials remain in storage.
— Details of the buildings and routes.
The materials handling systems followed by the spinning mills differ widely. Some of the mills, particularly modern mills, have been using appropriate materials handling equipment. At the same time, there are mills using outdated or more laborious systems.
Materials handling in a spinning mill broadly involves handling of raw material, intermediate products, wastes, finished goods, stores and maintenance equipment/tools. During fiber to yarn conversion, materials (raw material, laps, sliver, roving, yarn, finished goods and wastes) are stored at different places and transported between departments. Like any other manufacturing industry, spinning mills also require efficient materials handling system.
What is a forklift bale clamp attachment?
Forklift bale clamp attachments are fitted to a forklift mast in place of standard tynes and carriage.
The attachment is made up of two hydraulic clamps that can grip both sides of baled up products, whilst the attachments rear frame keeps the load in place during transit and lifting.

Common bale clamp applications
There are a wide variety of bale clamps manufactured for the safe lifting and transport of a wide variety of products and goods that can be utilized across multiple industries, these include:
- Agriculture
- Paper, recycling and packaging
- Wool
- Textile and synthetic materials manufacturing
Some common examples of how bale clamps assist the above industries are described below.
- Bale clamps can be used to carry almost any baled up product in farming and agriculture this may include bales of animal feed such as hay or raw materials such as cotton before and during processing
- Paper recycling and packaging manufacturers may use forklifts fitted with bale clamps to assist in the maneuvering pulp bales during the recycling process or to dispose of baled up waste at the completion of processing
- Textile and synthetic materials manufacturers may also utilize bale clamps for easy movement of products in the manufacturing process or to assist with storage of finished goods
Benefits of bale clamp attachments
- Where multiple bales are stacked on top of each other the thin profile of a bale clamps arms allows them to easily knife through tightly compacted loads to allow the easy removal of bales this ability increases operational safety, efficiency and productivity
- Safety is increased as a forklift operator can directly pick-up a bale load even if it is tightly compacted meaning the operator/employee doesn’t need manually maneuver the potentially large and heavy load into a position beforehand so the clamp can grip the load. In some storage situations bales can be stack from floor to ceiling, the clamp eliminates the potential of employees having to climb onto bales where they can potentially be struck or fall
- Efficiency is increased as the forklift with the clamp attached can complete lifting and transport operations all at once. There is no need for a secondary vehicle or action to be involved during the process as they forklift can pick-up, transport and safely drop-off the bale load all in one go decreasing the time taken to move each load leading to increased efficiency and productivity
- Pressure that is applied when gripping a load via a bale clamp can be smartly controlled to apply the correct pressure to provide a safe and sure grip whilst causing minimal if any damage to the product
- Damage to bales is also reduced due to the wide variety of clamp pads suitable for specific applications available on the market
- Bale clamps allow the quick and easy movement of non-palletized loads this can lead to monetary savings on freight as the weight of any necessary wooden or plastic pallets do not have to be factored into freight costs
- On top of monetary savings on freight extra storage space can also be reclaimed as bales are stacked directly on top of each other removing any pallets from storage stacks
Related Product
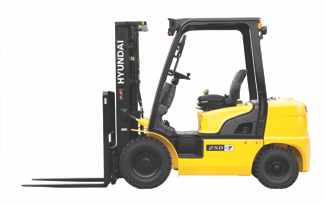
Forklift
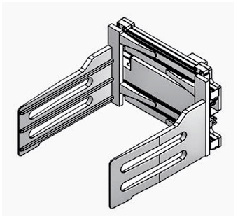